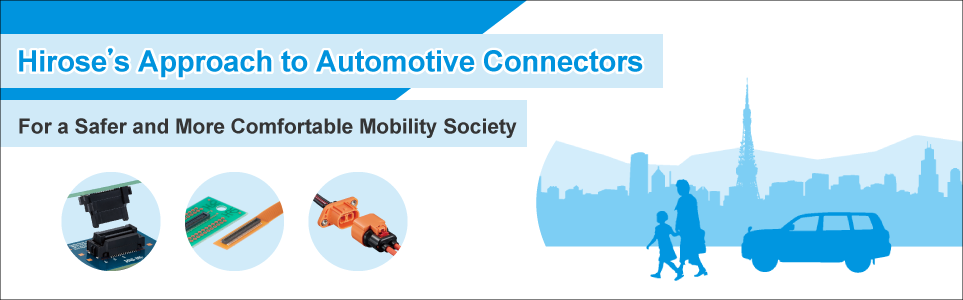
Hirose Electric contributes to the realization of a safer and more comfortable mobility society by providing high-quality automotive connectors. This section introduces some of our accomplishments in automotive connectors.
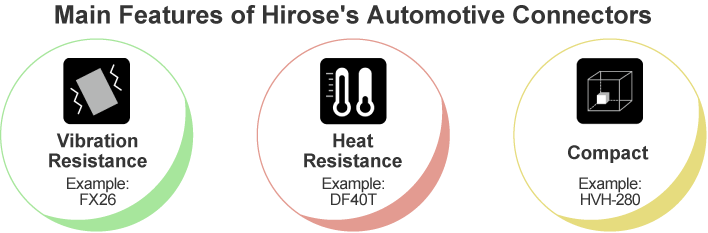
The connectors used in driving systems such as inverters must be durable enough to withstand vibration and high temperatures for a long period of time. Cameras and mmWave Radars used for driving assistance also require high reliability because of the high temperature exposure from direct sunlight and heat generation in the internal circuit.
We classify automotive connectors into three categories: (1) driveline connectors, (2) ADAS connectors, and (3) general automotive connectors. We conduct rigorous testing and propose only those connectors that satisfy our strict requirements.
Even if a product that has not passed the above tests is being considered by a customers for use in a vehicle, Hirose may ask them to reconsider if it is determined that sufficient reliability cannot be ensured. We believe that this will benefit our customers in the long run.
Stringent Test Conditions
Clears the most demanding tests required for automotive connectors. We provide high-quality automotive connectors that ensure safety.
*Example: ZE05 Series (Wire-to-Board Connector for Interface/Internal Connection)
*Test conditions vary depending on the connector.
Test Item | Test Method | |
---|---|---|
Mechanical Performance |
Vibration Resistance |
Conducting the test in front and rear, left and right, and up and down directions with the open-circuit voltage of 20mV Max. and the short-circuit current of 10 mA Max. Electrical discontinuity checked during testing. 88m/s2, 20 to 200 Hz |
Shock | Connector attached to shock absorber and checked for electrical discontinuity while shock is applied. Peak Acceleration: 981 m/s2, Operating Time: 6ms, 3 times in each direction | |
Environmental Performance |
Combined Environmental test | 300 cycles are performed with 1 cycle of energization then pausing in an atmosphere at 120℃. Vibration Conditions : 88m/s2, 20 to 200Hz Current : 1.2A (0.3sq) |
Temperature and Humidity Cycle |
Test conducted at -10 to 80℃/90% for 10 cycles with the contacts mated. During the test, a current of 10 mA is supplied to monitor the resistance variation. | |
Steady State Moisture Resistance |
14V applied in a thermostatic chamber with a high temperature of 80℃ and a high humidity of 90 to 95% RH then left for 96 hours. | |
Heat Resistance | Left at 140℃ for 120 hours with contacts mated. | |
Cold Resistance | Mate/unmate 5 times immediately after leaving the connector with mated contacts at -40℃ for 120 hours in a thermostatic chamber. | |
Heat, High Humidity and Current | 0.1mA DC applied to each pin in a thermostatic chamber with a high temperature of 85℃ and high humidity of 85% RH then left for 2,000 hours. | |
Corrosive Gas | Left for 96 hours in sulfurous acid gas at a concentration of 25ppm and a humidity of 75% RH or higher. Afterwards measurements are performed while in a mated condition. |
Introduction of Test Equipment
Yokohama Center
Shielded Room
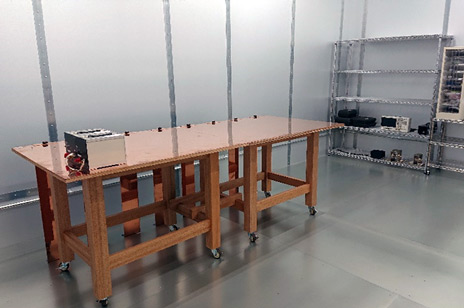
Anechoic Chamber
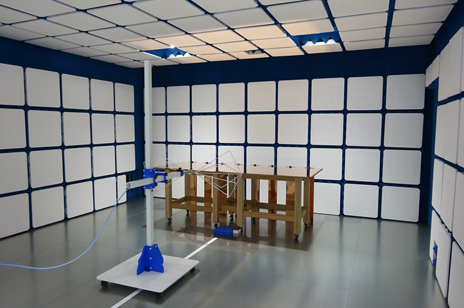
Hirose’s EMC laboratory (anechoic chamber and shielded room) applied for the ISO/IEC 17025 laboratory accreditation, granted on July 24, 2018, to improve the reliability of the EMC measurements made in our anechoic chamber. Furthermore our iNARTE-EMC certified engineers make sure that an environment in which EMC exams can be properly conducted is maintained.
Ichinoseki Testing Center
Largest Laboratory Amongst
Connector Manufacturers
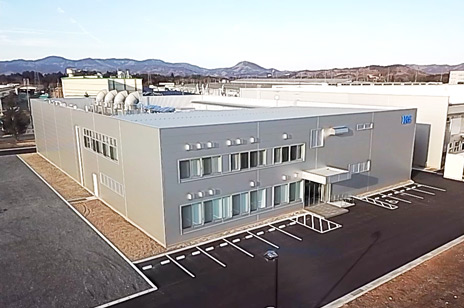
Testing Equipment Expanded to
More than 150 Units
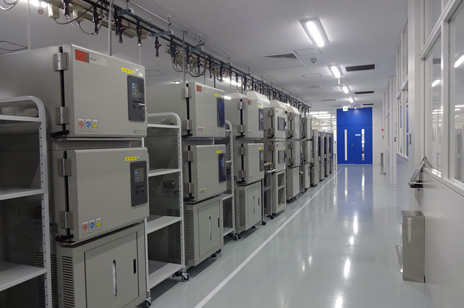
Complies with various tests required based component, such as combined vibration test (USCAR), water resistance test (IEC 60529/ISO 20653), salt water spray cycle test (IEC 60068 -2), temperature and humidity cycle test (USCAR). In 2018, we succeeded in reducing the test lead time by increasing the number of test machines.
In cases where the application will demand a high level of reliability, such as automotive, please contact a company representative for further information.